
Cyndi Rhoades on Breaking Textiles Back into Fashion Building Blocks
To keep fashion out of landfills, the target solution for much of the fashion industry today is circularity. Taking back garments and reusing them for new apparel or textiles lowers the need for new raw materials and cuts back on fashion’s wastefulness.
Worn Again Technologies founder Cyndi Rhoades is a frontrunner in this push for a closed loop. Her company is focused on turning used polyester and cotton into usable raw inputs for new fibers.
Shifting to a circular model is not a solo task. In the spirit of building these new systems together, Worn Again is one of the co-founders of World Circular Textiles Day, along with Circle Economy and University Arts London Centre for Circular Design. WCTD provides an opportunity for come together and celebrate progress in circularity and look at what still must be done to reach a goal of 100 percent circularity by 2050.
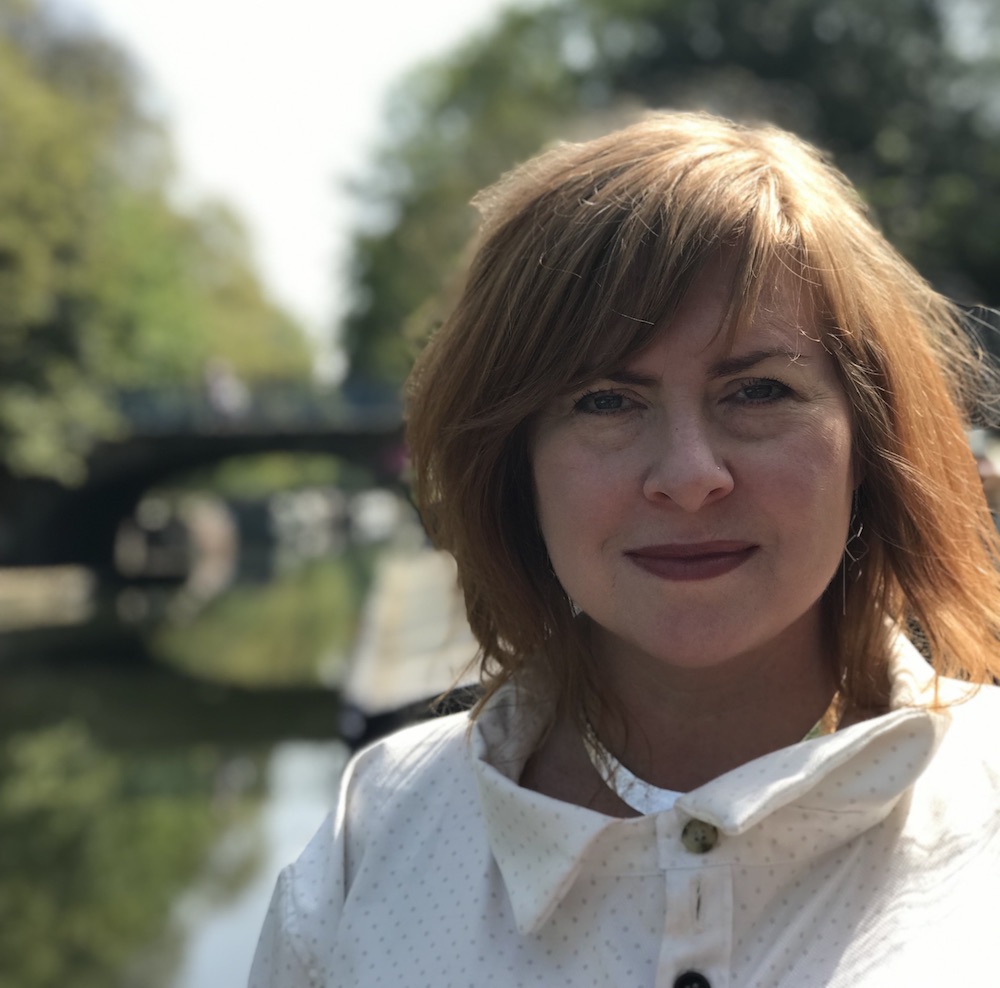
Fresh off the heels of the second World Circular Textiles Day celebration on Oct. 8, Carved in Blue caught up with Cyndi to discuss what is needed to facilitate more fashion recycling—from policy to collaboration.
Carved in Blue: When did you first start considering circular textiles? What prompted this?
Cyndi: It goes quite a way back to when I first started thinking about the growing mountains of textiles going to landfill every year, predominantly made up of polyester and cotton. After a few years of experimenting with upcycling, turning existing textiles back into second-life products, it became clear that if we wanted a comprehensive solution to textile waste, we needed to be looking at recycling at the molecular level.
The idea of raw materials recycling for polyester and cotton wasn’t new. Over a decade ago, a field trip to Teijin’s polyester depolymerization process in Matsuyama, Japan confirmed this. It was clear that technology was needed to enable the circularity of raw materials, but that it couldn’t happen without a systemic and joined up approach across the industry.
Carved in Blue: Do you think policy will accelerate change?
Cyndi: Without a doubt. Consumer demand to push for industry change gets the brands and retailers moving, but supportive policy that can incentivize the right behaviors by industry and local governments and cities, including waste prevention and increased collection rates, are needed.
Extended producer responsibility measures are going to play a big role in helping to put everyone on an even playing field. France is leading the way on this for textiles, and the European Waste Directive requiring a system for the separation of textiles from general waste by 2025 is going to be crucial. The key is in getting the policy change timeline aligned with the solutions. For instance, widespread textile-to-textile recycling processes need to be operational from 2025 onwards to be able to deal with the increased collection of non-rewearable textiles.
Carved in Blue: Textile circularity can be mechanical or chemical, and many players are entering the market. Where can designers get reliable facts?
Cyndi: That’s a tricky one because it’s a diverse and ever evolving space. There are multiple players coming to market and many solutions which are still in development. It also depends what materials are being used. A good place to start is by visiting the World Circular Textiles Day Knowledge Hub where we are building a database of facts, innovations and companies working in the field of mechanical and chemical recycling. It’s a kind of Wikipedia of circular textiles where anyone can add a new case study or initiative if anyone is missing.
Carved in Blue: How do you think we can explain textile circularity to children?
Cyndi: I like to use a Lego analogy. If you have a big pile of Lego at home, you can make pretty much anything that your imagination lets you. When you’re done with it, you return it to the Lego pile where it gets broken down back to its original bricks to be used again. You don’t throw the Lego bricks away and then go out and buy more; you use the same bricks over and over.
Going into more detail, after the creations are returned to the Lego pile and taken back down to single bricks, some special features like wheels, LEDs and moving parts might get put aside into another pile, and some of those bricks might need wiping down if they have jam on them before they are put back together into something new again. But that doesn’t mean we need to buy more Lego bricks—you can find some more in the toy cupboard!
Carved in Blue: What is your vision for WCTD in five years?
Cyndi: We could imagine that early stage, regional ecosystems have started to form, bringing more efficient flows of products and materials in pockets. Where service models have proliferated, more products are connected through product and materials ID platforms and are looping through multiple reuses. Textile returns are easy, and advanced textiles sorting facilities are processing effectively. A handful of textile-to-textile recycling plants that break down non-rewearable and non-reusable products are rejuvenating the first noticeable volume production runs of materials, going back into supply chains. New and better jobs are recognized and improvements across the value chain, all over the world, are taking place.
At this stage, we’ll be entering the next phase of circularity, what we call the Infrastructure and Rollout Years. And the WCTD global map that we’re building today, via data being uploaded to World Circular Textiles Day Knowledge Hub, will be exploding with activity as a result of industry working together to create an interconnected system of product and materials circulation. And the wider public is watching and participating.