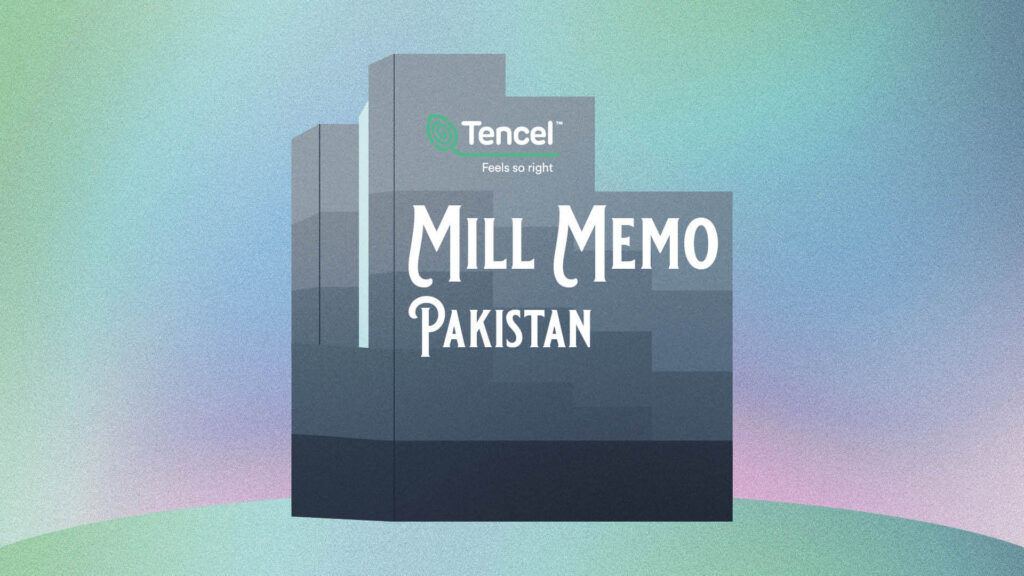
Mill Memo: Inside Pakistan Manufacturers’ Eco Efforts Part 2
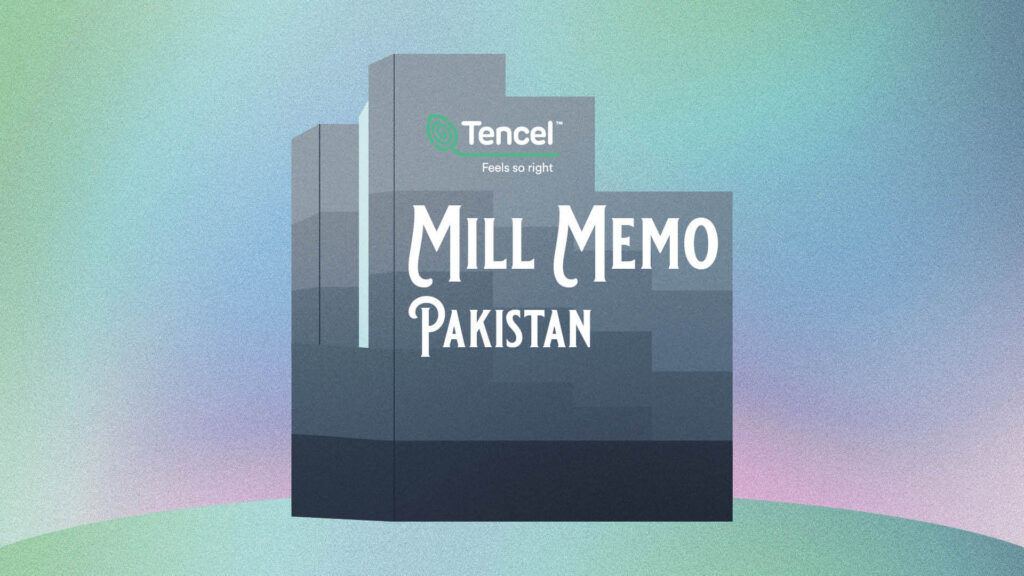
Denim mills are cleaning up jean production, and one of their moves is evolving raw material choices. Wood-based TENCEL™ fibers offer a lower impact alternative that comes with the added benefit of improved softness and durability.
Here, executives from Artistic Fabric Mills, Naveena Denim Limited, Naveena Denim Mills, Neela Blue, Rajby Textile, Saddiqsons Limited, SM Denim, Soorty and US Denim Mills discuss how they are using TENCEL™ lyocell and their climate action strategies.
ARTISTIC FABRIC MILLS
Farah Iqbal, director
Carved in Blue: Could you give an overview of your latest collections that include TENCEL™ fibers including REFIBRA™ technology?
Farah: At AFM, we are continuously working to strengthen and update our manufacturing processes, technology and sustainable practices.
In our sustainable fabric collection, we are using different kinds of regenerated cellulosic fiber, including the TENCEL™ and REFIBRA™ technology. TENCEL™ lyocell adds a soft hand and smooth touch to the denim quality with luster. To further enhance our products’ circularity, we are using 50 percent TENCEL™ blended with a larger percentage of recycled cotton fiber derived from the mill waste (pre-consumer waste) as well as post-consumer waste cotton (PCW). This makes the circular denim stronger and durable, as well as contributing to a more responsible, sustainable and environmentally friendly future.
Our Acadia (A4-050245) is the best example for this. It is a medium weight fabric, 11.25 oz, and contains upcycled fibers.
The following fabrics represent some of our best sellers that consist REFIBRA™ fibre in their composition: Visby (A4-050249/AS-584, 10.5 oz.) and Neoma (A4-050282/AS-582, 11 oz.).
Carved in Blue: Are you currently incorporating TENCEL™ Modal with Indigo Color technology or matte TENCEL™ into your denim?
Farah: Yes, in our recent collections, these fibers have played an important role.
We have designed a light- to medium-weight range, stretch fabric collection by incorporating TENCEL™ Modal with Indigo Color technology. The main advantage of using indigo modal is that since it is already indigo, we are saving chemicals, wastewater and energy, as we eliminate the need for the dyeing process.
For years, TENCEL™ has been used in denim due to many outstanding properties like softness and strength, and of course sustainability.
AFM recently partnered with the Lenzing Group, which introduced us to the world of matte TENCEL™ Lyocell, an engineered version of TENCEL™ with less sheen. These fibers are not only biodegradable and compostable, but also have been carefully designed to showcase versatility as it diminishes the glossy look in denim and to give the fabric a matte look. The closed-loop process used in the making also ensures that it is durable and eco-friendly.
Lastly, we have also designed fabrics with carbon-zero TENCEL™, which is a sustainable version of regular TENCEL™. It uses the renewable energy sources and new technologies to reduce the carbon footprint in the making. Our collection ranges from comfort to super stretch fabrics for this technology.
Carved in Blue: What top three things is your mill doing to combat climate change?
Farah: The high levels of electricity consumption in textile industries have always been a cause of concern for the environment. Therefore, AFM is switching to sustainable sources of electricity. We’re investing in solar panels to generate up to 1,000 kW of renewable solar energy, which will result in myriad benefits; especially, this new addition will help in reducing more than 1,200 tons of carbon dioxide emissions per year.
On the other hand, our aerial drying system saves up to 80 percent of energy. By loading around 1,600 units on the dryer at once, the environmental impact of jean manufacturing is significantly reduced.
AFM wants to play its part in managing water through responsible technology and production. Around the world, 844 million people still lack basic water services. In order to provide these people with basic and clean water services, AFM joins hands in fulfilling these goals by creating sustainable, zero-waste products with cutting-edge O2 and O3 tech.
This is a tri-factor combination that aims at saving every drop of water. In dyeing, finishing and laundry, we are saving up to 4,800 liters per meter of water. This comes up to saving an average of 95 percent per kg of our total water consumption. AFM is following Integrated Water Resources Management (IWRM) and treating water in a way that does not affect other sectors of society negatively.
Additionally, we are introducing our latest venture, AFM x OrganicCotton, in collaboration with WWF Pakistan, to farm organic cotton, creating income opportunities and livelihood for farmers in the region as well as adding transparency to the supply chain.
NAVEENA DENIM LIMITED (NDL)
Rashid Iqbal, executive director
Carved in Blue: Could you give an overview of your latest collections that include TENCEL™ fibers including REFIBRA™ technology?
Rashid: 100 percent TENCEL™ lyocell in ecru and indigo, slow fade concept with dyed modal, indigo-dyed modal, and The Bast Recast collection, which has TENCEL™, REFIBRA™ and modal.
Carved in Blue: Are you currently incorporating TENCEL™ Modal with Indigo Color technology or matte TENCEL™ into your denim?
Rashid: Yes, we have already incorporated TENCEL™ Modal with Indigo Color technology and matte TENCEL™ in our innovations. We will be showcasing our collection in the upcoming Kingpins Amsterdam exhibition.
Carved in Blue: What top three things is your mill doing to combat climate change?
Rashid: Water conservation: Zero liquid discharge, a rainwater harvesting system to maintain the water level in the city, a 50 percent reduction in water consumption in utility and production processes by 2018, as per goals and standards.
Chemical conservation: A caustic recovery plant has reduced our dependency on fresh chemicals and made the ETP process more efficient because the drainage of caustic has been reduced due to recycling.
Energy conservation: We invested in a solar power project with a capacity of 1.5 MW that will help us reduce our carbon footprint. We’re also using energy efficient technologies, new eco-friendly and less fuel-consuming engines, which are more efficient compared to the old ones. Our wind energy project in a coastal area has the capacity of 50 MW clean energy—this is in progress.
NAVEENA DENIM MILLS (NDM)
Aydan Tüzün, executive director of sales and marketing
Carved in Blue: Could you give an overview of your latest collections that include TENCEL™ fibers including REFIBRA™ technology?
Aydan: We use TENCEL™ fibers at every opportunity in our collections. For the latest collection, we produce mostly products in 10-13 oz. by washed weight and within our Retrosoft concept with a more authentic and marble look.
Our main blending partner is cotton. We make sure to include post-industrial and post-consumer waste cotton in our blends whenever we can.
For performance and comfort, we also blend with Lycra fiber and Lycra T400.
All these blends are also offered in EcoMade fibers as an option.

Carved in Blue: Are you currently incorporating TENCEL™ Modal with Indigo Color technology or matte TENCEL™ into your denim?
Aydan: We use TENCEL™ Modal with Indigo Color technology in different product development processes. It is indeed a super soft, sustainable and innovative fiber.
There is no need for an additional dyeing process since it is dyed from the melt, thus saving chemicals, water, energy and steam used in conventional indigo processes.
We are going to present our TENCEL™ and TENCEL™ Modal collection at Kingpins and Denim Days as a collaboration: TENCEL™ x Naveena x Endrime.

Carved in Blue: What top three things is your mill doing to combat climate change?
Aydan: At Naveena, we are constantly investing in new projects and machinery to continuously upgrade ourselves with the most efficient and environmentally friendly technologies to combat climate change.
Adding to our long-lasting commitment of investing in sustainable and clean energy, we are very proud to announce that Naveena Group has achieved financial close with the Government of Pakistan for its 50 MW wind power project in Jhimpir, Thatta, Sindh. The project will provide clean and cheap energy to the region and is scheduled to come online by March 2022.
We are also implementing a 2.2 MW solar energy generation and a new water recycling plant. Our target is recycling 90 percent of water by 2025.
Post-consumer waste is a really important area we invest in, too. PCW is one way that we can save cotton and recover all the wastages from the market. We have recently put in place a PCW recycling system that can process up to 5 tons of fabric per day, which can then be spun and woven back in with new cotton for completely new jeans.
NEELA BLUE
Umer Farooq, marketing & sales
Carved in Blue: Could you give an overview of your latest collections that include TENCEL™ fibers including REFIBRA™ technology?
Umer: Like every collection, this time around as well we have added many fabrics that include TENCEL™ Lyocell and REFIBRA™ technology.
Angel: 91 percent TENCEL™, 9 percent cotton
Hudson: 61 percent cotton, 39 percent TENCEL™
Howard: 65 percent cotton, 34 percent TENCEL, 1 percent Lycra
Annette: 34 percent cotton, 35 percent TENCEL™, 26.5 percent nylon, 4.5 percent Lycra
Steve: 52 percent cotton, 30 percent REFIBRA™ technology, 16 percent Coolmax EcoMade All Season, 2 percent Lycra
Carved in Blue: Are you currently incorporating TENCEL™ Modal with Indigo Color technology or matte TENCEL™ into your denim?
Umer: Yes, we have developed fabrics using TENCEL™ Modal with Indigo Color technology. It’s something novel and unique, and we are taking these developments on Kingpins Amsterdam this season to showcase our product innovation and capabilities to the denim community.
Enigma: 65 percent TENCEL(TM) modal, 29 percent nylon, 6 percent Lycra
Carved in Blue: What top three things is your mill doing to combat climate change?
Umer: Neela by Sapphire has always been at the leading end of innovation. Denim production requires a large amount of water during indigo dyeing and processing.
We are using a combination of different natural and regenerated fibers, which are eco-friendly and biodegradable to reduce the impact on the environment.
Moreover, our Purify Collection uses a special process to save more than 50 percent of water during indigo dyeing.
Lastly, we are actively working to reduce our carbon footprint across all processes and are targeting to be carbon neutral by 2030.
RAJBY TEXTILE
Muzammil Usmani, senior manager product development
Carved in Blue: Could you give an overview of your latest collections that include TENCEL™ fibers including REFIBRA™ technology?
Muzammil: In Rajby, we try to keep a close eye on what’s happening in the fashion world; this helps us in providing useful product solutions to our partners, targeting the eventual requirements of their end consumers. We launch conceptual collections every season to cater to the foreseen demands of our partner brands. The post-pandemic world is going through a settling process, and the previous two years have an immense impact on fashion choices. There is a rush of optimism and responsibility—people are looking for vintage aesthetics, bio-based materials, softness and premium basics.
Keeping above in mind, Rajby Textiles has recently launched a responsible denim collection, Eco-Fusion. This denim assortment promotes the use of alternative fibers while discouraging the use of virgin cotton. TENCEL™ fibers including REFIBRA™ and ECOVERO™ are two main fibers of this collection. These fibers are blended with Better Cotton, organic cotton, Marmara Original hemp, CiClo or Dual Fx EcoMade in different compositions and weight ranges from 8- 14 oz., targeting the desired goals in respective products.
The post-Covid work-from-home requirement has significantly increased the demand of loungewear. We tried to achieve the same level and comfort of wearing by blending TENCEL™ fibers in the right silhouettes. In this collection, the yarn counts used are a bit coarser than usual, achieving a softer, premium yet authentic look, which is full of denim character with the required ease of wearing.
Carved in Blue: Are you currently incorporating TENCEL™ Modal with Indigo Color technology or matte TENCEL™ into your denim?
Muzammil: Yes! We are already using TENCEL™ Modal with Indigo Color technology. The beauty of denim is all about the fades that a pair of jeans embrace over time, however, as we previously mentioned, that post-Covid impact on fashion choices is significantly different and we are anticipating a demand of forever stay colors in denim showing persistence of wearers’ character. No matter how the surroundings may behave, they will hold their ground and face the challenges. Foreseeing this demand, this product solution is something really interesting to explore, that’s why we have already tried it.
We have not used the matte TENCEL™ technology yet, however, we have plans to explore this for soft authentic developments.
Carved in Blue: What top three things is your mill doing to combat climate change?
Muzammil: The main initiatives that Rajby Textile has taken to combat climate change are mentioned below.
Cradle to Cradle Platinum and Gold Certifications: Since the last five years, Rajby Textile has been focusing a lot on the circular economy, and our efforts are evident in the form of certifications we have achieved in this period. Rajby Textileis the world’s first and only Cradle to Cradle Platinum certifiedfacility, which has a 100 percent biodegradable fabric line called Beluga. The facility is also Cradle to Cradle Gold Certified, and the products are marketed under the name of Green Mystery.
Water recycling and ZLD Zero Liquid Discharge project: Water stewardship is one of the major environmental requirements at the moment. In this regard, Rajby Textiles is recycling water from some manufacturing processes like singing and sanforizing in RO feed tank, which is approximately 5 percent of monthly consumption. Rajby Textiles is going to plan to recycle its discharge water through UF/MBR + RO base ZLD technology; that will save up to 70-80 percent inlet raw water and helps the system to maintain its water needs through a sustainable closed-loop process. This project is planned to be finalized by 2025.
Energy conservation: Rajby Textiles is efficiently using Powerhouse engines’ heat to produce approx. 18.11 percent of total steam required by the overall system. In this method, waste heat of generators is utilized as a fuel in Four WHR boilers instead of natural gas. Above sustainable steam generation process conserves up to 131.5 K m3/month approximately of natural gas.
Furthermore, Rajby Textiles is investing in more sustainable projects with the vision of environmental responsibility. Rajby Textiles is planning to utilize CO2 emissions from gas and coal boilers into equalization tank of ETP to maintain pH of inlet water instead of acid use that has low impact on following global climatic parameters, likewise ozone layer depletion (ODP), fresh aquatic ecotoxicity potential (FAETP), marine aquatic ecotoxicity potential (MAETP), terrestrial ecotoxicity potential (TETP), photochemical oxidation potential (PCOP), acidification potential (AP) and eutrophication potential (EP). Theoretically, 150,000 – 200,000 CO2e (in kgs) amount is required to treat sufficient inlet wastewater pH characteristics of equalization tank of ETP. Currently, this project is being in approval process.
SIDDIQSONS LIMITED
Ibrar Hussain, manager R&D fabrics
Carved in Blue: Could you give an overview of your latest collections that include TENCEL™ fibers including REFIBRA™ technology?
Ibrar: Here are pictures of our two products with REFIBRA™ and ECOVERO™ fibers blended with recycled polyester and elastane to give it zero-cotton composition.
Carved in Blue: What top three things is your mill doing to combat climate change?
Ibrar:
Green garment building: Our new green garment building, constructed exclusively for our denim division, is capable of making 1 million pieces per month and is starting in Fall 2022. The building has been approved and will meet the highest standards engineered to consume less energy and water.
Solar power: We have introduced clean and renewable energy generation that contributes to reducing environmental impacts and lowering emissions. Siddiqsons has a grid-tied system of 500 KW via which we supply electricity to the garment division. The energy acquired from solar accounts for 20 percent of the daily electricity to the garment division/facility.
Water stewardship:Our current reverse osmosis plants can generate up to 460,000 U.S. gallons per day, almost 65 percent of our daily consumption. We are in the process of upgrading to be able to generate 600,000 U.S. gallons per day, almost 85 percent of daily consumption.
SM DENIM
Rameez Rizvi, senior marketing manager
Carved in Blue: Could you give an overview of your latest collections that include TENCEL™ fibers including REFIBRA™ technology?
Rameez: Here at SM Denim, sustainability is our primary focus. The Impact series is our predominant product range that is further subdivided into different categories. The wood-based TENCEL™ fibers cover all categories, making them a true star of our collection.
Ever since the technology of TENCEL™ Lyocell with REFIBRA™ launched as the first commercially available cellulosic fiber with recycled content, it has changed the game for circularity in our collection.
We offer 100 percent TENCEL™ Lyocell with REFIBRA™ in the weight range of 2.75-7.25 oz. in our Featherlite collection to ramp up regular shirting fabric with a smooth hand feel to create a “silky and liquid” handle.
For qualities like softness and breathability in our Allure series, REFIBRA™ is integrated with cotton and Lycra EcoMade covering fabrics with weights starting from 3.75 oz. up to 11.00 oz.
For higher weights of 11 oz. in our Denovation series, we offer two different blends, where REFIBRA™ is either blended with cotton, ECOVERO™, Lycra T400 EcoMade or with modal, delivering soothing and tactile appeal and gaining traction as customers yearn for innovation and comforting touch.
Carved in Blue: Are you currently incorporating TENCEL™ Modal with Indigo Color technology or matte TENCEL™ into your denim?
Rameez: Currently, we are not using both technologies. However, we are in the midst of development while we strategize our supply chain.
TENCEL™ Modal with Indigo Color technology is our prime focus to expand our waterless and cotton-free collection of low-impact material choices, where lesser water and energy is utilized than conventional dyeing.
We plan to incorporate the new matte TENCEL™ Lyocell in our Featherlite fibers for versatility, functionality, comfort and lusterless finish.
The collection for both will be out for our customers by the third quarter of 2022.
Carved in Blue: What top three things is your mill doing to combat climate change?
Rameez: Eco-mindedness is not solely limited to a certain age. Consumers across all generations are considering the environmental impact of their purchases as they want to leave a better footprint behind for their generations to come.
SM Denim, in collaboration with different eco-conscious partners, enables the brands to help consumers make better choices by offering products that are low impact.
We at SM Denim embrace the responsibility to address the industrial challenges. Climate change is a global debate that has a huge impact on our day-to-day routine. Similarly, industries are playing their collective efforts in combating the climate change challenges by implementing eco-friendly strategies.
Out of all of our sustainable approaches, below are the three key highlights to take the pledge of being a responsible producer to the next level.
Sustainability goals: SM denim has worked diligently in accomplishing 10 out of the 17 SGD goals by achieving the following targets: clean water and energy; ZDHC certification; 25 percent waste reduction; 40 percent reduced carbon footprint; 100 percent caustic recovery and reuse; high-efficient gen-set generators with minimal carbon footprint; 90 percent of waste heat recovery.
We strive to accomplish the remaining goals as well in order to fully comply with the U.N.’s urgent call.
Traceability: Traceability and transparency in the textile supply chain are essential for achieving sustainability in the textile and fashion industry.
Today’s customer is mindful and wants to be aware of the product blockchain. In such a scenario, traceability comes into the picture. SM denim paints a transparent picture of all of our operations that are controlled and closely monitored to be aligned with our circular and sustainable goals.
From raw material to end product traceability data, including original certifications, materials used, where it is made, and impact savings.
Process sustainability: We take extreme focus on adapting eco-conscious processes.
From waterless dyeing to aniline-free dyeing and CleanKore technologies, we take every step consciously to promote sustainable practices ensuring a step further towards achieving a 100 percent circularity goal.
SOORTY
Noman Nadir, vice president research & product development denim
Carved in Blue: Could you give an overview of your latest collections that include TENCEL™ fibers including REFIBRA™ technology?
Noman: TENCEL™ is one of our most premium fibers for denim. Therefore, we are keen on incorporating it in many of our articles. We used TENCEL™ and modal and ECOVERO™ at every chance in our collections. We have developed a separate concept for our premium category.
Cotton Free: İn this theme, we have achieved some success ‘til now. İn this concept we have product with a blend of TENCEL™ Lyocell and ECOVERO™ in different weight ranges from 10-13 oz. Our cotton-free products have amazing soft touch, bright wash downs and ultimate comfort level. Initially we have started cotton-free products in rigid, but now we are expanding our product range in this category from stretch; we are even trying to develop super stretches as well in this category.
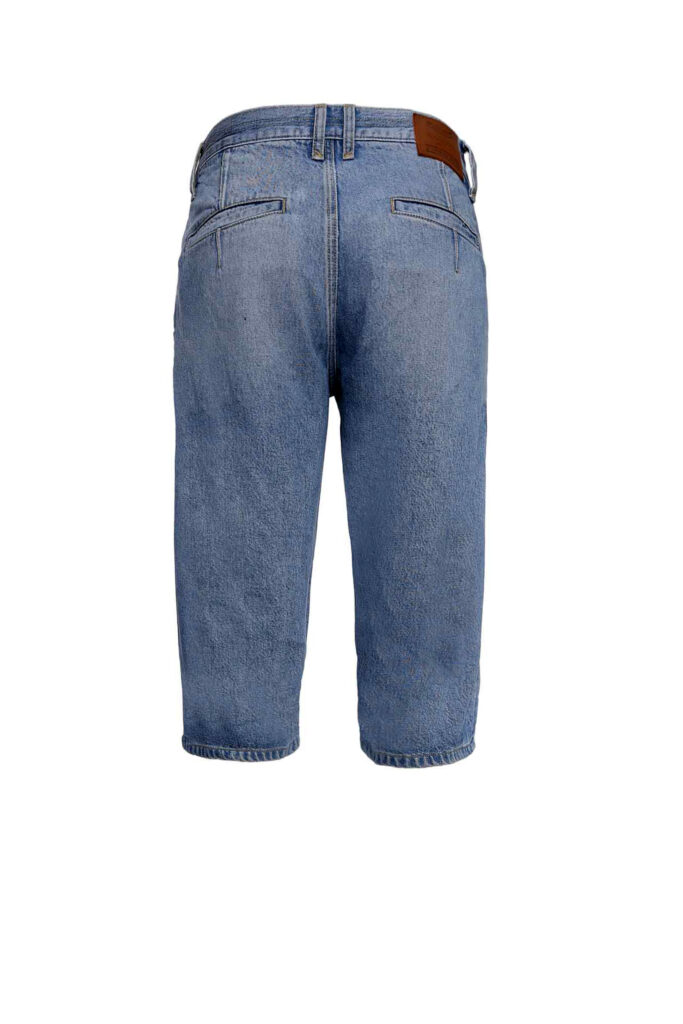
Cotton Less: We have done a great success making versions of our bestseller products with TENCEL™ blends and got good success.
Zero Virgin Cotton: This is a new concept we launched last season. We used REFIBRA™, hemp and PCW composition.

Longevity: It is a new concept that we will launch in this season. Here, we are using high-quality cotton and TENCEL™ fiber combinations, classics with much improved strengths and abrasion resistances. So that these jeans may last years’ long and won’t be thrown away after two seasons.

Carved in Blue: Are you currently incorporating TENCEL™ Modal with Indigo Color technology or matte TENCEL™ into your denim?
Noman: Yes, we made some development in indigo modal last season.
We have recently made sample of carbon-zero TENCEL™ and matte TENCEL™ with cotton blend product in indigo shade.
Price is also very important factor in all the new fiber innovation. If we are able to manage similar price like standard, then at least for carbon-zero TENCEL™, then we can think to switch all our production to carbon-zero TENCEL™.
Carved in Blue: What top three things is your mill doing to combat climate change?
Noman:
Using climate friendly fibers like TENCEL™, hemp, recycled polyester, organic cotton.
Making new investment for zero wastewater dyeing and finishing.
Setting up our own state-of-the-art shredding plant where we shred the used garment into fibers and use in our product.
US DENIM MILLS
Aleem Ahmad, senior manager research & business development
Carved in Blue: Could you give an overview of your latest collections that include TENCEL™ fibers including REFIBRA™ technology?
Aleem: We have developed fabrics with TENCEL™ Lyocell in diversified directions and with different blends. These fabrics are having aesthetics from super authentic crunch marbling character to hyper stretch premium denim with weight range from 8-14 oz. combined with Pima cotton, Lenzing Viscose, organic cotton, etc.; a complete product range for every age group.
Moving toward a sustainable world, we have started developing denim fabrics with sustainable materials, in which REFIBRA™ technology is playing a pivotal role. Fabrics having REFIBRA™ combined with sustainable fibers like ECOVERO™, hemp, PCW, PIW, CiCLO in rigid and comfort stretch constructions, give a confidence to customers that the products they are buying are not only fulfilling their fashion demands but also contributing in reduction of carbon footprint.
Carved in Blue: Are you currently incorporating TENCEL™ Modal with Indigo Color technology or matte TENCEL™ into your denim?
Aleem: We are under development process with these fibers and quite hopeful that they will be a good addition in our product range.
Carved in Blue: What top three things is your mill doing to combat climate change?
Aleem: Process and technology: At US Denim, we are continuing to shrink our carbon and non-renewable footprint by using sustainable practices. Our aim is to make fabrics with the most reliable and ecological processes to ensure adroit utilization of resources. Accordingly, we have developed a process, Eco-Zero, audited by BluWin (UK) that consumes 96 percent less water, 33 percent less steam and 43 percent less electricity than the conventional manufacturing processes.
Rapid Clean is an eco-efficient alternative technology for some of the most water-intensive and pollutant fabric finishing processes. Fabrics finished with Rapid Clean technology achieve the desired results with much less resources than the conventional process.
Renewable energy: U.S. Denim has installed solar plant of 1.206 MW capacity, which is fulfilling 4.2 percent of our total electricity requirement. In the future, we are aiming to increase the capacity of the solar plant to get 20 percent of the required electricity from it.
Sustainable materials, ZDHC compliant chemicals and water conservation: U.S. Denim has used 534,295 kg of PCW yarn and 894,243 kg of PIW yarn in 2021 production. We have achieved 95 percent compliant process chemical ZDHC score and targeting to achieve 100 percent by end of 2022. We have saved more than 273 million liters of water in 2021 as compared to 2020 by modification and optimization of processes.