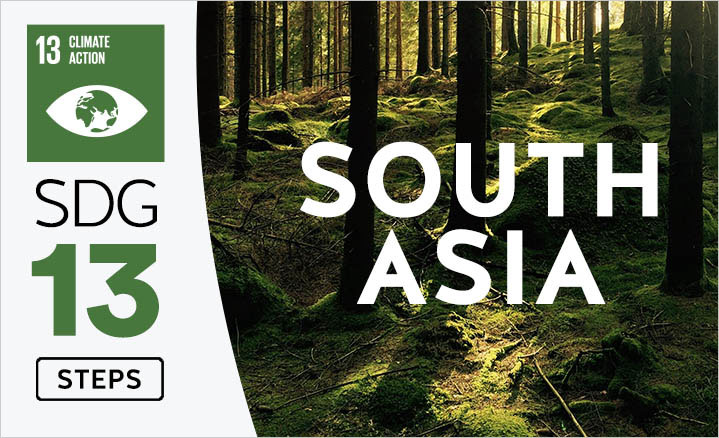
SDG 13 Steps: How South Asian Denim Mills are Embracing Climate Action
Reducing fashion’s carbon footprint has never been more imperative. A recent report by the Intergovernmental Panel on Climate Change indicates that without immediate and widespread intervention in shrinking emissions, it will be impossible to keep global warming limited to 1.5 degrees Celsius.
According to the United Nations, fashion is responsible for an estimated 2 to 8 percent of the world’s total carbon emissions. To tackle this issue, companies in the private sector are taking action. Signatories of the U.N.’s Fashion Industry Charter for Climate Action, including Lenzing, have committed to a goal of carbon neutrality by 2050.
In addition to signing on to the UNFCCC, Lenzing has reduced its own carbon impact through True Carbon Zero TENCEL™. For the fibers, we have reduced the carbon footprint of the production process as much as possible. Any carbon impact that cannot be avoided is then offset.
Around the globe, denim mills are innovating to address U.N. Sustainable Development Goal 13 on climate action. Read on to see how mills in India and Pakistan—including Indigo, KG Fabriks, Neela and Soorty—are reducing their carbon footprints.
INDIGO
Pakistan
At Indigo, technology and sustainability go hand in hand. The manufacturer is working to reduce carbon emissions from its production by focusing on facility upgrades. Solar power delivers up to a quarter of Indigo’s power needs, and a low fuel consumption generator limits the amount of oil needed. Inside, fluorescent lamps have been swapped out for lower energy LED lights. Indigo has also lowered the impact of its boilers with a condensing economizer, which reduces energy consumption and heat dissipation. Waste heat recovery boilers also use the residual exhaust heat from the generators to create steam.
In addition to the above, Indigo cares for the climate by planting trees that capture carbon dioxide.
KG FABRIKS
India
KG Fabriks took a speedy approach to sustainability, reaching major milestones and goals that most fashion firms had slated for 2030 prior to 2020.
In climate action, KG significantly reduced its electricity consumption per unit, with up to a 17.5 percent drop from 2018, which lowered its total emissions. The mill has also brought its purchase and usage of renewable energy to 20 percent of its total energy. Together with solar energy capture on the roof, this helps to power production sustainably. High efficiency looms also lower power needs.
Since it began using bio mass as fuel for its own operated power plant in 2018, KG has increased its usage by 39 percent. Biomass is defined as renewable organic material that would otherwise be landfilled or burned. Finally, the mill’s boilers have emission control devices, and other projects are underway to reduce air emissions.
KG is also using Carbon Zero TENCEL™ to further improve its footprint.
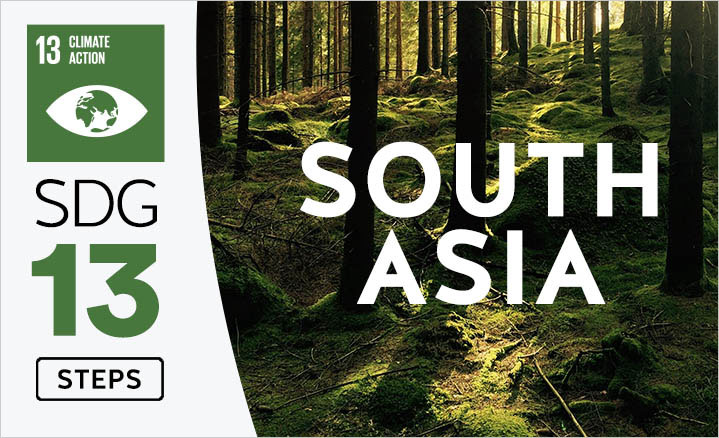
NEELA BLUE
Pakistan
Part of Sapphire Group, Neela Blue was founded in 2017 to change how denim is produced in Asia.
Neela Blue is using higher efficiency gas engines, reducing the amount of gas needed to supply the same amount of power. By changing out coal for biomass rice husk for steam production, Neela is also able to save on emissions. The mill has installed variable frequency drives on its engine auxiliaries to lower the auxiliary power.
Energy efficient lighting and optimal temperature settings for its evaporative cooling systems also lower the power use. Additionally, skylights have saved 50,000 kWh of electricity.
In its compressed air system, Neela has reduced the running power by lowering the setpoints to almost match operating pressure. It has also separated the air lines for cleaning air and processing air, allowing it to supply cleaning air at lower pressure. To further lower the power needs to produce compressed air, the mill has eliminated leaks in the system. Neela has created a caustic recovery plant that uses evaporation to recover caustic soda for reuse.
The mill is also supplying its steam boiler feed water tank by recovering condensation from machinery and hot water from its air compressor and caustic recovery plant.
In an effort to combat air pollution, Neela has also planted 5,000 indigenous plants.
SOORTY
Pakistan
Vertically integrated denim manufacturer Soorty equates innovation with “radical responsibility.” Its effort to develop lower impact denim includes recycling materials and engineering better laundry processing to save on water and energy.
Specifically around climate action, Soorty has prioritized green facilities. Factories in Pakistan and Bangladesh have achieved LEED certification. The mill’s DenimKind factory is LEED Platinum Certified, which Soorty says makes it the most sustainable denim production facility in the world at scale. At DenimKind, 95 percent of sunlight is captured to power the sewing floor, providing 35 percent of power needs. Energy is also delivered via natural gas generators.
The mill has worked with Green Story to measure and assess its environmental impact.
If you have your own climate action story to share, please email us at denim@lenzing.com